Epoxy Coating Near Me has become a popular option for coating concrete and cement floors. It is long-lasting and durable, making it a great choice for industrial and commercial spaces. It also helps to brighten the floor, reducing the need for extra lighting, which can save energy costs.
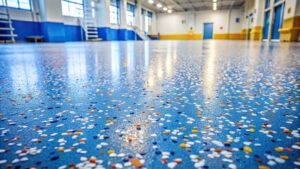
When applying epoxy, it is important to follow the manufacturer’s instructions. Surface preparation is vital to ensure proper adhesion and a smooth finish.
Epoxy floor coatings are among the most durable options for home and business floors. They can withstand heavy foot traffic and wheeled vehicles, as well as harsh chemicals. However, their durability can vary depending on the application. For example, epoxy flooring in manufacturing facilities may need to be recoated every 7 to 10 years, whereas an epoxy garage floor in a home might last 15 or more years.
To achieve a high-performance epoxy coating, the resin and hardener must be properly mixed. In addition, the coating must be applied in a thin layer and allowed to cure. During this time, the resins chemically react with each other to form a thermoset plastic. This reaction can take a few hours to several days, depending on the product and environmental conditions.
Many industrial and commercial settings require a high level of durability from their epoxy floors. This is because the floors are exposed to heavy foot and wheeled traffic, harsh chemicals, and other hazards. To prevent damage, it is important to implement a maintenance program that includes regular inspections and cleaning with non-acidic cleaners. In addition, it is a good idea to place walk-off mats or entry rugs in high-traffic areas.
Another option for increasing the durability of epoxy is to use a redox catalyst. These catalysts are able to convert epoxy compounds into phenolic novolac resins, which have excellent chemical and corrosion resistance. These redox catalysts can also be used to replace the curing agent in existing epoxy systems.
While the advantages of using epoxy coatings are clear, the disadvantages of such coatings must be considered before applying them in a commercial or residential environment. Epoxy is a high-performance material that requires proper installation by an experienced professional. It is crucial to follow all manufacturer’s instructions for mixing and application, as these factors will impact the performance of the epoxy coating.
In addition, the cost of an epoxy coating can be prohibitive for some companies. This is especially true for smaller businesses or those with limited budgets. Fortunately, there are alternative solutions to traditional epoxy coatings that can offer similar benefits at a lower price point.
Easy to apply
If you are planning to coat a concrete floor with epoxy, make sure the surface is clean and dry. If the concrete is new, wait 28 days before coating it. This allows the concrete to acclimate and cure properly before applying the epoxy. You should also remove any floor paint with sodium bicarbonate and a blasting unit to ensure the epoxy adheres properly. You can find these tools at a local hardware store or rent them from an equipment rental company.
To prepare the concrete for an epoxy coating, you must first etch it. This process opens up the pores of the concrete and ensures a strong bond with the epoxy. This can be done with muriatic acid, but it is safer to use a water-based acid wash called DRYLOK etch. This product is available from your local hardware store and can be applied with a brush or sprayer.
Whether you choose solvent-borne or water-based epoxies, it is important to follow all manufacturer’s preparation and application guidelines. If you are using solvent-borne epoxy, it is important to sand the floor and apply a minimum of 150-grit sandpaper to the substrate before coating. This will help the epoxy adhere to the substrate and prevent peeling or blisters.
Water-based epoxies should be used in warmer temperatures to avoid sagging. The lower viscosity of the epoxy will make it easier to work with, but you should be careful not to over-apply the material. To prevent this, make sure you apply the first coat in a thin film and only roll on additional coats after the previous coat has reached the green stage.
Before applying the epoxy, it is a good idea to test the area for moisture by pouring a small amount of water on the surface. If the water beads and does not soak in, the surface is likely sealed and is not suitable for an epoxy coating. It is also a good idea to wear a respirator and eye protection while working on the project. It is also a good idea to keep windows and doors closed while the epoxy dries.
Easy to remove
When epoxy is applied to a concrete surface, it can create an incredibly strong bond. But accidents happen, and sometimes a little bit of epoxy can get on the floor where it shouldn’t be. If this happens, there are ways to remove it quickly and easily without damaging the concrete surface.
Using the right solvent can help you get rid of unwanted epoxy in a few simple steps. First, blot the epoxy with a rag that has been saturated in acetone or isopropyl alcohol. You should do this in a well-ventilated area, as these solvents can produce harmful vapors that can damage your lungs and eyes. Make sure to wear gloves and a mask.
If you have a large area of epoxy to remove, you can use a flooring removal machine or shot blasting to break down the coating. Then, you can simply scrape the remaining coating with a putty knife or scraper. This method is effective for thick coatings and also helps prepare the substrate for new coatings or finishes.
Another option is to use a chemical stripper to remove the epoxy coating. This can be purchased online or from your local home improvement store. Before you use it, however, make sure to read the label for safety precautions and directions. It is a good idea to test the stripper on a small area of the floor to ensure that it won’t damage the concrete underneath.
Lastly, you can also use heat to get rid of epoxy. This is especially helpful if you have a smaller area of epoxy that needs to be removed from the concrete surface. This process involves applying a heat gun to the epoxy, which causes it to soften. Once the epoxy has softened, you can then scrape it off with a plastic scraper.
The most important thing to remember when removing epoxy is to have the right equipment and follow proper safety protocols. It is also a good idea to have fire extinguishers and emergency response procedures in place. You should also keep your work areas clean and organized, and provide safety signs, barricades, and non-slip floor mats to prevent accidents and injuries during the process.
Versatility
Epoxy coatings are highly versatile and can be used on a variety of surfaces. They are easy to clean and are resistant to chemicals, impact, abrasion, and UV light. They can be used for commercial or industrial floors, walkways, and traffic-bearing areas. They are also slip-resistant, which is great for safety and aesthetics. Epoxy floor coatings are a durable and cost-effective choice for any space.
Epoxies can be used as adhesives, sealers, and coatings. They can be applied to metals, glass, wood, plastics, and ceramics, as well as other materials. They offer excellent electrical insulation, mechanical strength, and resistance to heat, chemicals, solvents, and saltwater. They are also easy to apply and can be applied either by hand or by machine.
The versatility of epoxy makes it an excellent choice for a number of different applications, from commercial and industrial spaces to residential garage floors. Epoxy is also a great choice for kitchens, bathrooms, and pool decks, as it is durable and water-resistant. In addition, it is anti-slip and offers UV protection, which can protect the surface from fading. It can be painted to match any décor or color scheme, and it is easy to clean and maintain.
Although epoxy is an excellent material for protecting surfaces, it requires specific environmental conditions to be successful. The ideal ambient conditions are critical for proper cleaning, preparation, and application of the first coat. If these conditions are not available, the protective coating will fail to perform as expected and may deteriorate quickly. For example, a steel surface that has been coated with epoxy in uncontrolled environments can experience flash corrosion within 30 minutes.
For this reason, professional contractors use temporary climate control solutions to create the optimal ambient conditions for each stage of the epoxy surface coating process. These solutions can be used in shipyards, power plants, construction sites, and more. In addition to providing superior performance, they save time and money by eliminating the need for costly reapplications.
Researchers have been working to improve the performance of epoxy by adding nanoparticles. For instance, Pourhashem et al. developed an epoxy-based coating reinforced with amino-functionalized graphene quantum dots (GQDs) for mild steel corrosion protection. The GQDs were obtained by hydrothermal synthesis using citric acid as a precursor, and their silanization was performed with the standard toluene route. They were dispersed in acetone, mixed with the epoxy filler and polyamide hardener, and then dried by solvent evaporation.